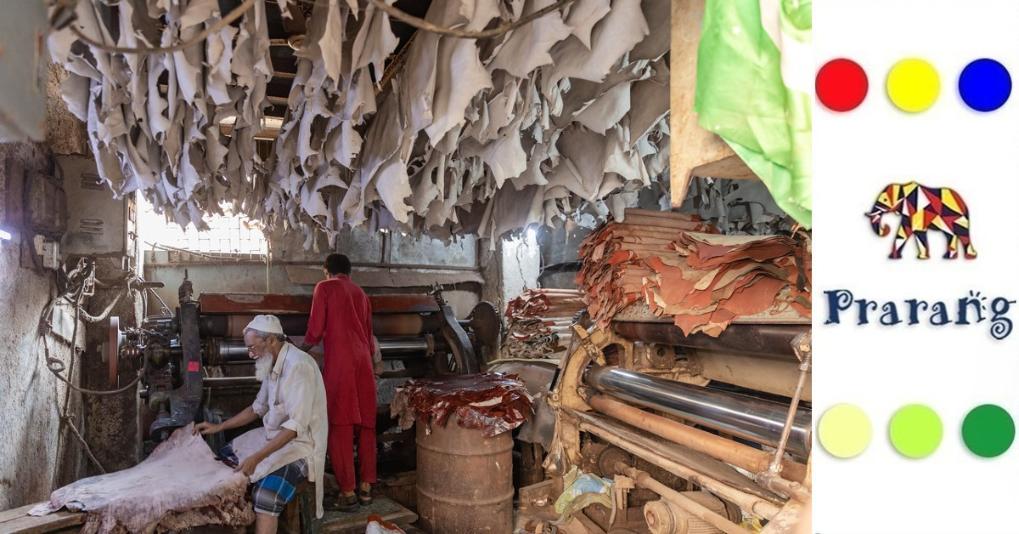
Post Viewership from Post Date to 22- Mar-2025 (31st) Day | ||||
---|---|---|---|---|
City Subscribers (FB+App) | Website (Direct+Google) | Total | ||
2725 | 51 | 2776 | ||
* Please see metrics definition on bottom of this page. |
रामपुर के कुछ लोग, यह जानते होंगे कि, उत्तर प्रदेश, भारत के चमड़े उद्योग में एक प्रमुख स्थान रखता है।यहाँ कानपुर और आगरा को उनके चमड़े के वस्त्रों और जूतों के उत्पादन के लिए जाना जाता है।कानपुर का चमड़ा उद्योग, जिसमें चमड़ा पकाने वाले कारखाने और चमड़े के सामान बनाने वाले निर्माता शामिल हैं, कानपुर और उन्नाव ज़िलों में लगभग दस लाख लोगों को सीधे और अप्रत्यक्ष रूप से रोज़गार प्रदान करती है।
तो आज हम भारत की चमड़े की उद्योग की वर्तमान आर्थिक स्थिति पर नज़र डालेंगे। इसके बाद, हम भारत में वस्त्र बनाने में इस्तेमाल होने वाले विभिन्न प्रकार के चमड़े के बारे में जानेंगे। फिर हम, भारत में चमड़े की जैकेट बनाने की प्रक्रिया के बारे में विस्तार से सीखेंगे। इसके बाद हम कानपुर की चमड़े की उद्योग पर कुछ प्रकाश डालेंगे। अंत में, हम जानेंगे कि, कानपुर कैसे भारत में चमड़ा उत्पादन का केंद्र बन गया।
भारत के चमड़ा उद्योग की वर्तमान स्थिति
1.भारत का चमड़ा उद्योग, देश की अर्थव्यवस्था में एक अहम भूमिका निभाता है और यह विदेशी मुद्रा कमाने वाले शीर्ष दस क्षेत्रों में शामिल है। साल 2020-21 में, जूते, चमड़ा और इससे बने उत्पादों का निर्यात 3.68 अरब अमेरिकी डॉलर के करीब था।
2. भारत के पास, विश्व की 20% गाय-भैंस, 11% बकरियों और भेड़ों की आबादी है, जो इस उद्योग को कच्चे माल का बड़ा आधार प्रदान करती है। इसके साथ, कुशल कामगार, आधुनिक तकनीक, और अंतरराष्ट्रीय पर्यावरण मानकों के पालन से यह उद्योग और मज़बूत हुआ है।
3.यहाँ के चमड़ा उद्योग में लगभग 4.42 मिलियन (44 लाख) लोग काम करते हैं, जिनमें से 30% महिलाएं हैं। भारत दुनिया में चमड़े के परिधानों (leather garments) का दूसरा सबसे बड़ा निर्यातक है। इसके अलावा, यह सैडलरी (saddlery) और हार्नेस ( harness) का तीसरा और चमड़े के सामानों का चौथा सबसे बड़ा निर्यातक है।
4. इस उद्योग के मुख्य उत्पादन केंद्र तमिलनाडु (चेन्नई, वेल्लोर), उत्तर प्रदेश (कानपुर, आगरा), पश्चिम बंगाल (कोलकाता), और महाराष्ट्र (मुंबई) जैसे राज्यों में फैले हुए हैं। ये केंद्र, भारत को चमड़ा उत्पादन में वैश्विक स्तर पर एक मज़बूत स्थान दिलाते हैं।
5. भारत का चमड़ा उद्योग, लगातार बढ़ रहा है, जिसमें आधुनिक उत्पादन इकाइयां, पर्यावरण-अनुकूल चमड़ा तैयार करने की प्रक्रिया, और शोध, डिज़ाइन व विकास के लिए संस्थागत समर्थन शामिल हैं।
भारत में कपड़ों के निर्माण में उपयोग होने वाले चमड़े के प्रकार
भारत का चमड़ा उद्योग, अपनी कारीगरी और गुणवत्ता के लिए प्रसिद्ध है। खासकर चमड़े की जैकेट्स की मांग बहुत अधिक है। कपड़ों की गुणवत्ता, टिकाऊपन और सुंदरता, उपयोग होने वाले चमड़े के प्रकार पर निर्भर करता है । यहाँ हम भारत में आमतौर पर इस्तेमाल होने वाले चमड़े के प्रकारों को आसान भाषा में समझेंगे।
1. फ़ुल-ग्रेन चमड़ा (Full grain leather)
फ़ुल-ग्रेन चमड़ा, चमड़े की दुनिया का सबसे अच्छा और मज़बूत प्रकार माना जाता है। इसे बिना रगड़े या साफ़ किए पूरे चमड़े से बनाया जाता है, जिससे इसका प्राकृतिक रूप और मज़बूती बनी रहती है।
फ़ुल-ग्रेन चमड़ा, बहुत टिकाऊ होता है और समय के साथ, इसका रंग और चमक में बेहतरी आती है। यह नमी से भी बचाव करता है। हालांकि, यह शुरुआत में थोड़ा सख़्त होता है और अन्य प्रकारों की तुलना में महंगा होता है।
इस चमड़े का उपयोग महंगे और लंबे समय तक चलने वाले कपड़ों में किया जाता है। यह लक्ज़री ब्रांड्स की पहली पसंद होता है।
2. टॉप-ग्रेन चमड़ा (Top grain leather)
टॉप-ग्रेन चमड़ा, फ़ुल-ग्रेन से थोड़ा कम गुणवत्ता वाला होता है, लेकिन फिर भी, यह काफ़ी अच्छा माना जाता है। इसकी सतह को साफ़ और चिकना बनाने के लिए रगड़ा और सुधार किया जाता है।
यह फ़ुल-ग्रेन से ज़्यादा नरम और लचीला होता है। इसका लुक एक समान और चमकदार होता है। हालांकि, यह थोड़ा कम टिकाऊ होता है और इसका प्राकृतिक रूप, समय के साथ ज़्यादा नहीं बदलता।
इसका उपयोग, मध्यम कीमत वाली जैकेट्स और उन कपड़ों में किया जाता है, जो गुणवत्ता और सस्ते दाम का मेल चाहते हैं।
3. जेन्यून चमड़ा (Genuine leather)
जेन्यून चमड़ा, चमड़े की निचली परतों से बनाया जाता है और इसे जोड़कर एक सामग्री का रूप दिया जाता है। यह फ़ुल-ग्रेन और टॉप-ग्रेन की तुलना में कम टिकाऊ होता है, लेकिन इसकी कीमत कम होती है।
यह किफ़ायती और आसानी से उपलब्ध होता है। हालांकि, यह ज़्यादा टिकाऊ नहीं होता और जल्दी ख़राब हो सकता है।
इस चमड़े का उपयोग उन कपड़ों में होता है, जो बजट में रहने वाले ग्राहकों के लिए बनाए जाते हैं।
4. स्वीड चमड़ा (Suede leather)
स्वीड चमड़ा, चमड़े की निचली सतह से बनाया जाता है। इसका मुलायम और अलग प्रकार का रेशेदार लुक इसे ख़ास बनाता है।
स्वीड, स्टाइलिश, मुलायम और लचीला होता है। यह ट्रेंडी और विंटेज डिज़ाइन्स के लिए बेहतरीन विकल्प है। हालांकि, यह आसानी से दाग-धब्बों और पानी से खराब हो सकता है। अन्य प्रकारों के मुकाबले यह कम टिकाऊ होता है।
स्वीड का इस्तेमाल कैशुअल जैकेट्स और फ़ैशनेबल कपड़ों में किया जाता है।
भारत में चमड़े की जैकिटें कैसे बनाई जाती हैं ?
चमड़े की जैकेट बनाने की प्रक्रिया में कई चरण होते हैं। यहां हम आपको यह बताने जा रहे हैं कि भारत में इसे कैसे बनाया जाता है:
1.) जैकेट डिज़ाइन - चमड़े की जैकेट बनाने वाले निर्माता, आमतौर पर डिज़ाइनरों को काम पर रखते हैं, जो पैटर्न बनाते हैं। इन पैटर्न्स के ज़रिए, कपड़े बनाए जाते हैं। कंप्यूटराइज़्ड मशीनें (computerised machines), डिज़ाइनों को सरकारी आकार तालिकाओं के अनुसार ग्रेड करती हैं, जो शरीर की ऊंचाई और वज़न के हिसाब से आकार तय करती हैं। फिर कंप्यूटर, उन डिज़ाइनों से अलग-अलग आकार के पैटर्न तैयार करता है।
2.) कटाई - तैयार चमड़े को चलने वाली टेबल्स पर रखा जाता है, जिनको स्प्रेडर्स (spreaders) कहते हैं। आधुनिक तकनीक से एक साथ कई परतों को काटा जा सकता है, लेकिन चमड़े को एक बार में एक परत ही काटा जाता है। पैटर्न को चमड़े पर रखा जाता है। इसे दो तरीकों से किया जाता है: या तो पैटर्न को चमड़े पर पिन किया जाता है, या फिर उसे टेलर की चॉक से चिन्हित किया जाता है।
3.) जैकेट के विभिन्न हिस्सों को जोड़ना - चमड़े की जैकेट को इस प्रकार जोड़ा जाता है: सबसे पहले साइडों को पीछे के हिस्से से, फिर आस्तीनों के नीचे के सीवे को जोड़ा जाता है और फिर उनको आर्महोल्स (armholes) से जोड़ा जाता है। जैकेट के डिज़ाइन के हिसाब से कॉलर, कफ़्स, बटनहोल्स, बटन, ज़िप्पर और पॉकेट्स को जोड़ा जाता है। पैच पॉकेट्स को पहले साइड पीस में सिला जाता है, फिर उन्हें बैक से जोड़ा जाता है। सामान्यतः जैकेट के हर हिस्से में लाइनिंग मटेरियल पहले जोड़ा जाता है और फिर उसे जैकेट में सिला जाता है।
4.) मोल्डिंग और प्रेसिंग - कई प्रेसिंग प्रक्रियाओं में हीट, स्टीम और ब्लॉकिंग का इस्तेमाल किया जाता है, जो चमड़े को एक जैकेट के रूप में बदलने में मदद करती हैं। बक प्रेस में कंट्रोल्स और गेज होते हैं, जो स्टीम और दबाव को नियंत्रित करते हैं। इससे जैकेट को अपनी खास आकृति मिलती है, चाहे वह बॉम्बर जैकेट हो या ब्लेज़र स्टाइल जैकेट। कॉलर और कफ़्स के आसपास, कर्व्ड ब्लॉक्स लगाए जाते हैं, फिर उन पर गर्मी दी जाती है। ब्लॉक्स हटाए जाते हैं और कॉलर और कफ़्स को एक खास आकार में ढाल लिया जाता है।
5.) अंतिम निरीक्षण - जैकेट को फ़ैक्ट्री से बाहर भेजने से पहले हर जैकेट का हाथ से निरीक्षण किया जाता है। फिर पूरी तरह से तैयार जैकेट को प्लास्टिक बैग में रखा जाता है, फिर उसे कार्टन में पैक किया जाता है और रीटेलर को भेजा जाता है।
इस प्रकार से चमड़े की जैकेट्स बनाई जाती हैं, जो एकदम सुंदर और मज़बूत होती हैं।
कानपुर के चमड़ा उद्योग का परिचय
कानपुर शहर, देश के चमड़ा उद्योग का सबसे बड़ा केंद्र है। ब्रिटिश शासन के दौरान, इस क्षेत्र में बड़ी संख्या में सैनिकों की मौजूदगी के कारण विभिन्न चमड़े के उत्पादों की प्राकृतिक मांग पैदा हुई थी। फ़ैक्ट्रियों के बनने से पहले, गांव के कारीगर कुटीर उद्योग के रूप में चमड़े के सामान बनाते थे, जो स्थानीय ज़रूरतों को पूरा करते थे। ये उत्पाद, मुख्य रूप से गाड़ी, बैलगाड़ी के सामान, सवारी के सामान और बर्तन बनाने के काम आते थे।
कानपुर में कई प्रकार के चमड़े के उत्पाद बनते हैं, जैसे जूते, बेल्ट, पर्स, चप्पल, कपड़े और सवारी के सामान। यह शहर, भारत के कुल चमड़े और उससे संबंधित उत्पादों के निर्यात का 20 प्रतिशत से ज़्यादा योगदान देता है। यहां बने उत्पाद, कई देशों में निर्यात किए जाते हैं, जिनमें अमेरिका और यूरोपीय देशों के अलावा, कई अन्य देश भी शामिल हैं।
कानपुर कैसे बना भारत में चमड़ा उत्पादन का केंद्र ?
कानपुर, जिसे कभी ‘पूर्वी मैनचेस्टर’ के नाम से जाना जाता था, भारत में चमड़ा उद्योग का प्रमुख केंद्र है। 19वीं सदी के प्रारंभ में, जब ब्रिटिश सेनाओं ने कानपुर को अपना मुख्यालय बनाया, तो यहां चमड़े के उत्पादों की मांग बढ़ गई, जैसे जूते, पालकी और जीन. इससे कानपुर में दो महत्वपूर्ण उद्योग स्थापित हुए - सरकारी हार्नेस और सैडल कारखाना और कॉपर ऐलन एंड कंपनी, जिन्होंने ब्रिटिश सेनाओं को चमड़े के उत्पादों की आपूर्ति की और दोनों विश्वयुद्धों के दौरान, महत्वपूर्ण योगदान दिया।
भारत की स्वतंत्रता के बाद, चमड़े के उत्पादों की मांग में कमी आई, लेकिन 1970 के दशक में, इस उद्योग का पुनरुद्धार हुआ। आज कानपुर में 400 से अधिक पंजीकृत टैनरी हैं, जिनमें से कई प्रकार के चमड़े का उत्पादन होता है। कानपुर का चमड़ा उद्योग न केवल भारत में बल्कि विदेशों में भी प्रसिद्ध है। 2003-04 में कुल निर्यात 1636 करोड़ रुपये था, जो अगले दो वर्षों में बढ़कर 2000 करोड़ रुपये से अधिक हो गया।
कानपुर के चमड़ा उत्पादन में 95% हिस्सा है, विशेष रूप से दोहन (harness) और काठी (saddle) में। यहां के प्रमुख इलाकों जैसे जाजमऊ में अधिकांश टैनरी स्थित हैं। कानपुर का चमड़ा उद्योग 2 लाख से अधिक लोगों को रोज़गार प्रदान करता है, और इसके निर्यात का भारत में 15% हिस्सा है।
संदर्भ
मुख्य चित्र : धारावी, मुंबई में चमड़े की एक कार्यशाला (Wikimedia)
A. City Subscribers (FB + App) - This is the Total city-based unique subscribers from the Prarang Hindi FB page and the Prarang App who reached this specific post.
B. Website (Google + Direct) - This is the Total viewership of readers who reached this post directly through their browsers and via Google search.
C. Total Viewership — This is the Sum of all Subscribers (FB+App), Website (Google+Direct), Email, and Instagram who reached this Prarang post/page.
D. The Reach (Viewership) - The reach on the post is updated either on the 6th day from the day of posting or on the completion (Day 31 or 32) of one month from the day of posting.